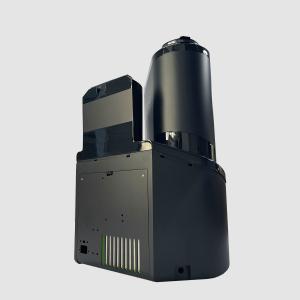
Add to Cart
CNC turning
CNC turning is a machining process that involves the removal of material from a rotating workpiece using a cutting tool. It is primarily used for creating cylindrical parts with external and internal features.
In CNC turning, the workpiece is typically a bar or rod of metal or plastic material that is secured in a chuck and rotated at high speeds. The cutting tool is then brought into contact with the rotating workpiece, and material is gradually removed to achieve the desired shape and dimensions.
CNC Turning Tolerances | |
we machine CNC turning lathe parts to meet tight tolerance requirements. Based on your design, our CNC lattes can reach tolerances of up to ±0.005”. Our standard tolerances for CNC milled metals is ISO 2768-m and ISO 2768-c for plastics. | |
Type | CNC Turning Tolerances |
Linear dimension | ±0.025 mm-±0.001 inch |
Hole diameters | ±0.025 mm-±0.001 inch |
Shaft diameters | ±0.025 mm-±0.001 inch |
Part size limit | 950 * 550 * 480 mm-37.0 * 21.5 * 18.5 inch |
CNC turning machines can perform a variety of operations, including facing, turning, grooving, threading, and drilling. The cutting tool can move along both the axial direction (parallel to the workpiece's rotational axis) and the radial direction (perpendicular to the rotational axis). This allows for the creation of complex internal and external geometries, as well as the generation of different types of threads.
The advantages of CNC turning include:
Versatility: CNC turning can produce a wide range of cylindrical parts with various diameters, lengths, and features. It can create parts with intricate internal cavities, external profiles, and precise threading.
Efficiency: CNC turning is a highly efficient process, as it allows for continuous machining once the setup is complete. This enables fast production rates and shorter lead times.
Accuracy and Repeatability: CNC turning machines are capable of achieving high levels of accuracy and repeatability, resulting in consistent and precise parts. This is particularly important for components that require tight tolerances.
Cost-Effectiveness: CNC turning can be a cost-effective solution for producing cylindrical parts, especially when compared to other machining processes like milling or grinding. It minimizes material waste and reduces the need for secondary operations.
Scalability: CNC turning is suitable for both small-scale production runs and larger quantities. It can efficiently produce prototypes, custom parts, and components for mass production.
CNC turning is widely used in industries such as automotive, aerospace, manufacturing, and electronics, where cylindrical parts are common. It offers a reliable and efficient method for producing parts with complex internal and external geometries and various thread types.
CNC turning as a form of precision machining where material is removed by a cutter that makes contact with a spinning workpiece. The movement of the machinery is controlled by computer instructions, ensuring precise and repeatable results.
CNC turning differs from CNC milling in that the cutting tool rotates and is directed at the stationary workpiece from multiple angles. In CNC turning, the workpiece is rotated in a chuck, allowing for the creation of round or tubular shapes. This process is particularly effective in achieving accurate rounded surfaces that may be challenging to achieve with CNC milling or other methods.
A CNC lathe machine used for turning typically has a turret where the tooling is mounted. This turret can be programmed to execute specific movements and remove material from the raw materials, ultimately forming the desired 3D model or part.
Similar to CNC milling, CNC turning is suitable for both rapid prototyping and the production of end-use parts. Its precision and efficiency make it a valuable process for manufacturing components with round or tubular geometries.
By utilizing CNC turning, manufacturers can achieve high-quality results, optimize production time, and produce prototypes or final parts with accuracy and repeatability.
CNC turning as a subtractive manufacturing process where a stationary cutting tool removes material by making contact with the spinning workpiece to shape it according to the desired specifications.
In CNC turning, a blank bar of stock material is securely held in the chuck of the spindle and rotated along with the spindle itself. The cutting tool, which remains stationary, then removes material from the workpiece to create the desired shape. The movement of the machinery is precisely controlled by computer instructions, ensuring accuracy and repeatability in the manufacturing process.
CNC turning is particularly suited for creating round or tubular shapes and achieving highly accurate rounded surfaces. The rotational nature of the process allows for the creation of cylindrical components, such as shafts, cylinders, and other rotational symmetry parts, with excellent precision.
CNC Machining Tolerances and Standards | ||
With precision CNC machining services, Barana Rapid is your ideal partner to create precision machined prototypes and parts. Our standard CNC machining tolerances for metals is ISO 2768-f and for plastics is ISO 2768-m. We can also achieve special tolerances as long as you indicate your requirements for your drawing. | ||
Standards | CNC Milling | CNC Turning |
Maximum Part Size | 2000x1500x600 mm | 200x500 mm |
Minimum Part Size | 4x4 mm 0.1*0.4 in | 2x2 mm 0.079x0.079 in |
Minimum Feature Size | Φ 0. 50 mm Φ 0. 00197 in | Φ 0. 50 mm Φ 0. 00197 in |
Standar Tolerances | Metals: ISO 2768-f Plastics: ISO 2768-m | Metals: ISO 2768-f Plastics: ISO 2768-m |
Hole Diameters | +/- 0. 025 mm +/- 0. 001 in. | +/- 0. 025 mm +/- 0. 001 in. |
Linear Dimension | +/- 0. 025 mm +/- 0. 001 in | +/- 0. 025 mm +/- 0. 001 in |
Edge Condition | Sharp corner will be removed in the form of a chamfer or radius. The size of the chamfer, or resulting radii, must be indicated on the drawing. | |
Shaft Diameters | +/- 0. 025 mm +/- 0. 001 in. | +/- 0. 025 mm +/- 0. 001 in. |
Threads and Tapped Holes | Diameter: Φ 1. 5-5 mm, depth: 3×diameter Diameter: Φ 5 mm or more, depth: 4-6×diameter | Diameter: Φ 1. 5-5 mm, depth: 3×diameter Diameter: Φ 5 mm or more, depth: 4-6×diameter |
Types of Thread | Barana Rapid can produce threads of any specification and size required by our customers. | |
Text | Minimum width of 0. 5 mm, depth of 0. 1 mm | Barana Rapid can use laser marking to create standard text for CNC turned parts. |
Lead Time | 3 business days | 3 business days |
Comparatively, CNC milling involves the rotation of the cutting tool while the workpiece remains stationary, allowing for the creation of more complex shapes and features. CNC milling is typically used for producing parts with intricate geometries, such as slots, pockets, and complex 3D profiles.
Understanding the difference between CNC milling and CNC turning is valuable in determining the appropriate machining process based on the desired outcome and the specific requirements of the part or component.
If you're looking for further information on the distinctions between CNC milling and CNC turning, you can refer to the link you provided or explore additional resources that delve into the topic in more detail.
Materials for CNC Turning Parts | |||
Our CNC turning processes are compatible with a wide range of materials, including machine-grade metals and plastics. Depending on your applications, we can create precise rapid prototypes and low-volume production from various superior-quality materials. Check out some of the common materials for your CNC turning projects. | |||
![]() | ALuminum Aluminum is a highly ductile metal, making it easy to machining. The material has a good strength-to-weight ratio and is available in many types for a range of applications. | ALuminum | |
Machinable Material Types | AL 6061, AL6063,AL6082,AL7075 | ||
Lead Time | 3 days | ||
Tolerances | ±0.01mm | ||
Max part size | 200 x 80 x 100 cm | ||
![]() | Copper Copper displays excellent thermal conductivity, electrical conductivity and plasticity. It is also highly ductile, corrosion resistant and can be easily welded. | Copper | |
Wall Thickness | 0.75 mm | ||
Lead Time | 3 days | ||
Tolerances | ±0.01mm | ||
Max part size | 200 x 80 x 100 cm | ||
![]() | Brass Brass has desirable properties for a number of applications. It is low friction, has excellent electrical conductivity and has a golden (brass) appearance. | Brass | |
Wall Thickness | 0.75 mm | ||
Lead Time | 3 days | ||
Tolerances | ±0.01mm | ||
Max part size | 200 x 80 x 100 cm | ||
![]() | Stainless Steel Stainless steel is the low carbon steel that offers many properties that are sought after for industrial applications. Stainless steel typically contains a minimum of 10% chromium by weight. | Stainless Steel | |
Wall Thickness | 0.75 mm | ||
Lead Time | 3 days | ||
Tolerances | ±0.01mm | ||
Max part size | 200 x 80 x 100 cm | ||
![]() | Titanium Titanium has a number of material properties that make it the ideal metal for demanding applications. These properties include excellent resistance to corrosion, chemicals and extreme temperatures. The metal also has an excellent strength-to-weight ratio. | Titanium | |
Wall Thickness | 0.75 mm | ||
Lead Time | 3 days | ||
Tolerances | ±0.01mm | ||
Max part size | 200 x 80 x 100 cm | ||
![]() | Plastics Plastics are also a very popular option for CNC machining because of its wide choices, relatively lower price, and significantly faster machining time needed. We provide all common plastics for CNC machining services. | Plastics | |
Machinable Material Types | ABS,PC,PMMA,PTFE,PVDF,POM,PA | ||
Lead Time | 3 days | ||
Tolerances | ±0.01mm | ||
Max part size | 200 x 80 x 100 cm |
What Separates Barana Rapid’s Inspection Processes from the Rest?
Careful measurement, inspection and testing are necessary to ensure the conformance of your parts. We perform multiple inspections at every step of the product development journey, from incoming material verification to final 3D scanning. You will receive complete digital files and Certificates of Compliance so you can meet your own regulatory and performance goals.
An International Team with Unparalleled Experience
Quality inspection relies not only upon using advanced digital equipment but also having highly trained personnel with years of experience. As parts become more complex and tolerances more demanding for advanced applications, precision measurements conducted by professionals are the only way to ensure perfection.
Inspections and Review for Every Stage of Production
To ensure quality from start to finish, Barana Rapid provides the following inspection and review services:
Extensive incoming materials verification
Design for manufacturing reviews for all quotes provided
Contract reviews upon receipt of POs
First article and in-process inspections
Final inspections and testing with reports and certifications as required